
The concept of using LBW in AM is adopted from welding where wobbling has been used for many years. In welding, it is used to generate wider seams which allow for covering larger gaps. Furthermore, wobbling allows for the fixing of imperfections and often results in less thermal stresses, distortion, and greater ductility. In addition to that, the multiple passing (overlapping, thermal cycling) of locations by the laser beam are known to have a considerable influence on the micro-structure often improving the mechanical properties of the manufactured part.

The figure above schematically illustrates the Laser Beam Wobbling (LBW) concept. While the laser moves along a straight trajectory, an oscillating pattern allows for an extended trajectory width. Typical wobble patterns include circle (depicted above), linear, figure of eight, and infinity patterns, operating at frequencies (f) typically in the range 300Hz to 1KHz. It is noteworthy to mention that the overall forward speed of the laser trajectory is not considerably influenced by the wobbling, and thus, the manufacturing speed tends to be the same as with traditional, linear scanning trajectories.
In metal Laser Powder Bed Fusion (LPBF), LBW is novel and relatively unexplored. If at all, it is mentioned in the context of post-processing techniques (surface finishing) rather than in the context of manufacturing parts. However, very few recent publications clearly hint toward advanced scanning trajectories that may be used in LPBF machines to attain better material properties and improved productivity.
The melt pool and its influence on manufactured part quality
The melt pool shape, size, and temperature gradients have considerable influence on the final, manufactured part quality including micro-structure, porosity, surface roughness, ductility, and material strength. More specifically, research has found that enhanced weld quality can be achieved through better control of thermal gradients which results in a reduction in cracking and porosity and can become a real option to produce tailored mechanical properties for parts.
Considering the above, there remains room to better understand advanced scanning techniques that may influence the melt pool and part quality.
The role of simulation in exploring LBW methods
Finite Element (FE) based simulation has been applied successfully over the last decade in AM to study details of the process on different scales including detailed studies of melt pool formation on the meso- and micro-scale. A commonly used approach is to feed the key process parameters such as laser power, laser spot size, scanning speed, and hatch spacing into the model and obtain time-dependent thermo-mechanical and morphological results as demonstrated here in this article.
However, the use of FE simulation to explore the effects of LBW for LPBF is unexplored and allows room for novel studies. In the section, we like to demonstrate how LBW can be explored with the use of the AdditiveLabRESEARCH software.
The concept for using the AdditiveLabRESEARCH software to study the effect of LBW for LPBF
To demonstrate the use of our software to study the effect of LBW, we have created the two meso-scale FE models as depicted below. As material AlSi10Mg was assumed.

The figure above shows the FE meshes of the meso-scale LPBF simulation model using a traditional scanning pattern (left) and the model using a wobble pattern (right). The laser power, laser spot size, and region covered by the laser (width x length) are the same. The laser speed has been adjusted for both models to finish scanning the covered region at the same time.
Results
The section below presents some of the results that can be extracted from the simulation model in order to assess the pros and cons of the different scanning strategies.
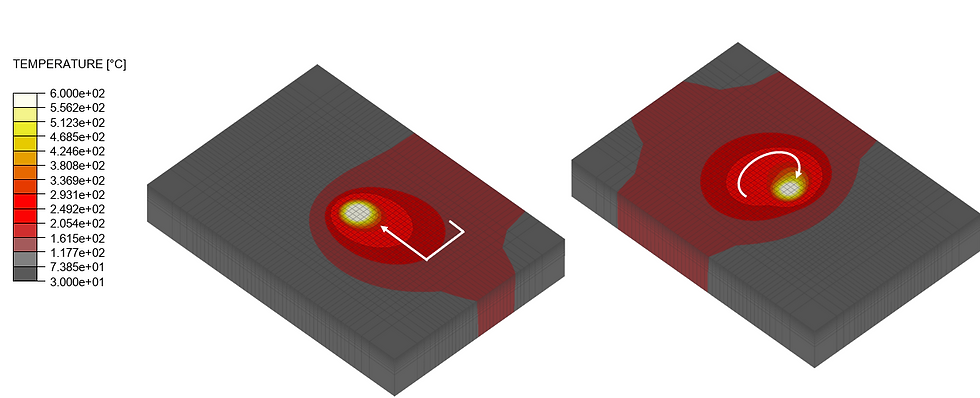
The figure above shows the temperature results of the meso-scale LPBF simulation model using a traditional scanning pattern (left) and the model using a wobble pattern (right) halfway through the simulation.

The figure above shows the temperature histories of the traditional hatching (blue) and the wobble (red) simulation model measured centrally at the top surface of the simulation model. Note: the difference in max. temperature comes from the different scanning speeds to have both simulations completing at the same time.
The figure above shows the temperature progressions at a central location at the top surface of the simulation models. The utilization of the traditional pattern characterizes the temperatures with lower temperatures (~100-150 degC) when passing and with a high thermal gradient resulting in a maximum temperatures of ~1000 degC when directly running over the specified location. On the contrary, the temperatures of the wobble pattern is characterised by a continuously increasing temperature with moderate gradients with localized temperature "spikes" whenever the laser passes really closely or over the specified location.
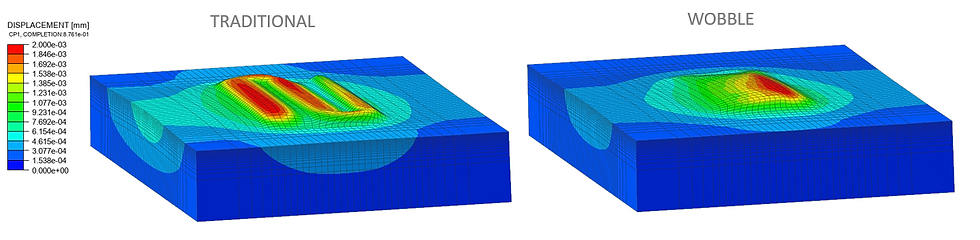
The figure above shows the displacements of the traditional hatching (left) and the wobble (right) simulation model at completion of the simulation (after cool down). The displacements are exaggerated with a factor of 40.
The displacements at the completion of the thermo-mechanical simulation models indicated a considerable difference. It appears that the exaggerated display of displacements shows a rough peak-to-valley transition perpendicular to the longer trajectories in the traditional pattern which is not visible in the wobble pattern model. This may indicate the benefits of smoother surfaces with the wobble technique.
Conclusion
In this study, we compared FE simulation results of a traditional scanning technique with a conceptual Laser Beam Wobble (LBW) technique. LBW is well utilized in traditional welding to deduce cracking, porosity and enables users to produce tailored mechanical properties for parts. LBW applications in Additive Manufacturing (AM) are unexplored and only very little literature exists. However, due to the similarities of welding and Laser Powder Bed Fusion AM it is possible to similarly take advantage of LBW. While this conceptual study with the AdditiveLabRESEARCH software by no means is exhaustive, it demonstrates some of the results that can be obtained when investigating novel LBW techniques.
Do you have questions or need more information? Please reach out to us via info@additive-lab.com
Commenti